The older generation of opticians often asked if they had glass or crystal lenses, and scoffed at the resin lenses that we generally wear today. Because when they first came into contact with resin lenses, the coating technology of resin lenses was not developed enough, and there were disadvantages such as being not wear-resistant and easy to leave stains. In addition, many manufacturers and retailers have a backlog of glass lenses that need to be sold, so the shortcomings of resin lenses have been exaggerated for a period of time.
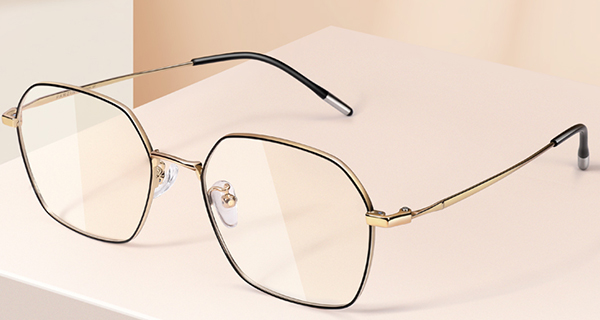
Glass lenses do have the advantages of wear resistance and high refractive index. But its weight and fragility caused it to be replaced by resin lenses. With the advancement of science and technology, the coating technology developed by the spectacle lens manufacturing industry has solved many problems at the beginning of the invention of resin lenses. This article will give you a brief introduction to the coating of spectacle lenses, so that you can more objectively understand the coatings of the lenses you wear and their development history.
We generally have three kinds of coatings on lenses, namely, wear-resistant coating, anti-reflection coating, and anti-fouling coating. Different coating layers use different principles. We generally know that the background color of both resin lenses and glass lenses is colorless, and the faint colors on our general lenses are brought about by these layers.
Wear-resistant film
Compared with glass lenses (the main component of glass is silicon dioxide, which is an inorganic material), the surface of spectacle lenses made of organic materials is easy to wear. There are two types of scratches on the surface of spectacle lenses that can be observed through microscope observation. One is made of small sand and gravel. Although the scratches are shallow and small, the wearer is not easily affected, but when such scratches accumulate to a certain extent , the incident light scattering phenomenon caused by scratches will greatly affect the wearer's vision. There is also a large scratch caused by larger gravel or other hard objects. This kind of scratch is deep and the periphery is rough. If the scratch is in the center of the lens, it will affect the wearer's vision. Therefore, the wear-resistant film came into being.
The wear-resistant film has also undergone several generations of development. At first, it originated in the 1970s. At that time, it was believed that the glass was wear-resistant because of its high hardness, so in order to make the resin lens have the same wear resistance, the vacuum coating method was used. , a layer of quartz material is plated on the surface of the organic lens. However, due to the different thermal expansion coefficients of the two materials, the coating is easy to fall off and brittle, and the wear resistance effect is not good. A new generation of technology will appear every ten years in the future, and the current wear-resistant coating is a mixed film layer of organic matrix and inorganic particles. The former improves the toughness of the wear-resistant film, and the latter increases the hardness. The reasonable combination of the two achieves a good wear-resistant effect.
Anti-reflection coating
The lenses we wear are the same as flat mirrors, and the light incident on the surface of the glasses lenses will also reflect. In some specific cases, the reflections produced by our lenses can affect not only the wearer but also the person looking at the wearer, and at critical times, this phenomenon can lead to major safety incidents. Therefore, in order to avoid the harm caused by this phenomenon, anti-reflection films have been developed.
Anti-reflection coatings are based on the fluctuation and interference of light. To put it simply, the anti-reflection film is coated on the surface of the spectacle lens, so that the reflected light generated on the front and rear surfaces of the film interferes with each other, thereby offsetting the reflected light and achieving the effect of anti-reflection.
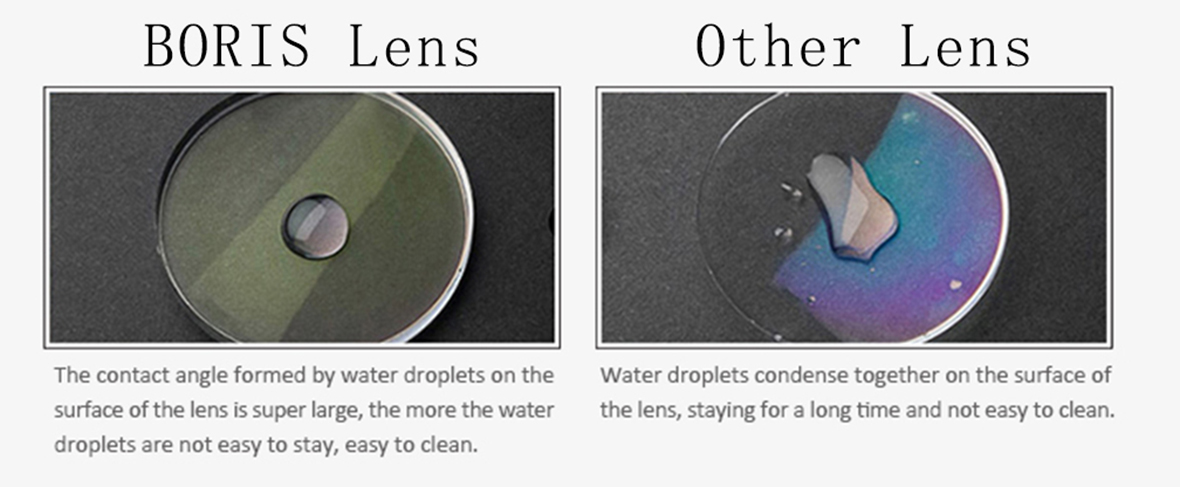
Anti-fouling film
After the lens surface is coated with anti-reflection coating, it is particularly easy to leave stains. This will greatly reduce the "anti-reflection ability" and visual ability of the lens. The reason for this is that the anti-reflection coating layer has a microporous structure, so some fine dust and oil stains are easily left on the lens surface. The solution to this phenomenon is to coat a top film on the top of the anti-reflection film, and in order not to reduce the ability of the anti-reflection film, the anti-fouling thickness of this layer needs to be very thin.
A good lens should have a composite film formed by these three layers, and in order to enhance the anti-reflection ability, there should be multiple layers of anti-reflection films superimposed. Generally speaking, the thickness of the wear-resistant layer is 3~5um, the multilayer anti-reflection film is about 0.3~0.5um, and the thinnest antifouling film is 0.005um~0.01um. The order of the film from the inside to the outside is the wear-resistant coating, the multi-layer anti-reflection coating and the anti-fouling film.
Post time: Jun-08-2022